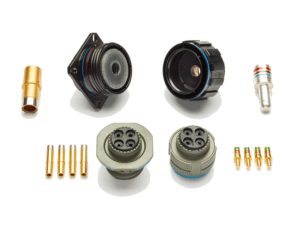
ZEUS power connectors are available in various contact configurations and layouts.
Using IEH Hyperboloid contact technology and MIL-DTL-38999 III architecture the connectors can withstand high vibration with no loss of continuity. Zeus Power Connectors can also be supplied with filtered power contacts.
Other layouts can be designed to customer specification with applications up to 260 Amps DC possible.
These power connectors have been developed to fill the gap where a standard catalogue item is not able to meet high power and high vibration requirements. Apollo has designed a range of connectors to meet these specific needs.
Power Connector Technology
ZEUS high power connectors use Hyperboloid contact technology with MIL-DTL-38999 III architecture to allow currents of up to 260 Amps DC to be passed.
The Hyperboloid contact is an advanced design that satisfies performance requirements previously considered impossible. The distinguishing feature of the socket is the hyperboloid shaped sleeve formed by straight wires strung at an angle to the longitudinal axis. When the pin is inserted into this sleeve, the wires stretch, well within elastic limits, to accommodate it. In so doing, the wires wrap themselves around the pin providing several continuous line contact paths.
The Hyperboloid contact design provides:
- Very Low Insertion Force: Common sizes #22 and on average under one ounce per contact.
- Extraordinary Resistance to Shock & Vibration: Tests exceeding 300 g’s without discontinuity.
- Duty Cycle Exceeding 100,000 Mate/De-mate: The burnishing action of the wires on the pin surface is non-destructive.
- Low Contact Resistance: Excellent interface exhibiting low contact resistance (often less than 1/2 of MIL Spec. allowances).
- Improved Current Carrying Capacity: The low contact resistance gives a lower °C rise from ambient under load. This feature often allows the user to operate the same size contact under higher load.
- Highest Reliability: The contact design has proven itself to be the leading design for integrity and reliability.
Materials
- Pin Contacts: PhBr per ASTM B139, BeCu per ASTM B196 or B197, or Cu alloy
- Socket Contacts: Contact Wires: BeCu per ASTM B196, or B197 Termination: PhBr per ASTM B139 or Cu alloy
- Support Elements: Cu alloy
Finishes
- Pin Contacts: Gold per ASTM B488 Type II, Class 0.25, 0.50, or 1.27, Code C, over Nickel, 0.000050 min., per SAE AMS QQ-N-290 over Copper per SAE AMS 2418 or ASTM B734
- Socket Contacts: Contact Wires: Gold per ASTM B488 Type II, Class 1.27, Code C, over Nickel, 0.000050 min., per SAE AMS QQ-N-290 over Copper per SAE AMS 2418 or ASTM 734
- Termination: Gold per ASTM B488 Type II, Class 0.25, or 0.50, Code C, over Nickel, 0.000050 min., per SAE AMS QQ-N-290 over Copper per SAE AMS 2418 or ASTM B734 Support Elements: Nickel, 0.000050 min., over Copper
Performance
- Contact Resistance: See Chart – EIA-364-06 & MIL-DTL-55302 (par. 4.5.5)
- Temperature: -65°C to +125°C (-86°F to +257°F)
- Mating Force: See Chart – MIL-DTL-55302 (par. 4.5.4)
- De-mating Force: See Chart – MIL-DTL-55302 (par. 4.5.4)
- Solderability: (Where Applicable) IPC/EIA J-STD-002, Category 3
- Humidity: IAW EIA-364-31, Method IV, except 7A & 7B (not required)
- Vibration: IAW EIA-364-28 & MIL-DTL-55302 (par. 4.5.10)
- Shock: IAW EIA-364-27 & MIL-DTL-55302 (par. 4.5.14)
- Salt Spray: IAW EIA-364-26 & MIL-DTL-55302 (par. 4.5.11)
- Temperature Cycling: IAW EIA-364-32 & MIL-DTL-55302 (par. 4.5.13)